IPS – Answers to Frequently Asked Questions
FAQ Section –
Creating Knowledge
Creating Knowledge
Our IPS FAQ page provides you with a comprehensive insight into the fields of vibratory finishing, process media, painting technology, and special machine engineering, as well as automation and conveying technology. Here, we have compactly prepared the ten central questions on these intriguing topics for you. From the basics to specific details, we offer a concentrated source for you to quickly inform yourself about the essential aspects of these important areas of industrial production. Regardless of whether you are a newcomer or already have expertise, our compilations provide an efficient way to familiarize yourself with the world of vibratory finishing, process media, painting technology, and special machine engineering.
Topic Overview
Fundamentals of Vibratory Finishing:
What you've always wanted to know about vibratory finishing - 10 questions and answers
Vibratory finishing is a surface finishing process that involves moving workpieces in a rotating drum or container along with media, water, and compounds to smooth surfaces, break edges, and polish parts.
Various types of media are used in vibratory finishing, such as ceramic balls, plastic chips, or steel balls, depending on the specific requirements of the surface treatment.
Vibratory finishing offers benefits such as achieving uniform surface quality, removing burrs and sharp edges, smoothing workpiece surfaces, polishing jewelry, and increasing dimensional accuracy.
Vibratory finishing is suitable for a variety of workpieces, including metal parts, plastic components, jewelry, precision components, and more.
Factors such as the choice of media, the composition of the compounds, the amount of fill in the container, the rotational speed, and the processing time influence the vibratory finishing process.
In dry vibratory finishing, workpieces and media are processed without liquid lubricants. In wet vibratory finishing, processing is carried out in a liquid mixture of water and compounds.
It is important to wear personal protective equipment such as safety glasses and gloves to minimize potential hazards from media and liquids.
Compounds such as cleaners, rust inhibitors, and polishes can improve the effectiveness of the vibratory finishing process and achieve the desired surface quality.
Yes, vibratory finishing can reach its limits with very complex workpieces with tight tolerances and delicate structures. In such cases, other surface finishing methods may be better suited.
Vibratory finishing is used in the industry for applications such as deburring castings, polishing jewelry, smoothing workpiece surfaces, rounding edges on metal parts, and preparing surfaces before coating.
Summary:
Vibratory finishing, also known as barreling or vibratory polishing, is a widely used process in the surface treatment of workpieces. By using rotating drums or containers in which workpieces are moved along with media, water, and special additives, this technique enables smoothing, polishing, and deburring of surfaces. In this context, the following section answers basic questions about vibratory finishing to provide a better understanding of its applications, benefits, and procedures.
Process Media in Vibratory Finishing
The 10 most important questions and answers about process media summarized for you
In vibratory finishing, grinding bodies, grinding media additives, and water are primarily used as process media.
Grinding bodies are abrasive particles that move together with the workpieces in the grinding drum. They generate friction and help to remove surface irregularities and smooth them out.
Various types of grinding bodies are used, such as ceramic balls, plastic chips, steel balls, steel pins, and natural materials like wood or walnut shells.
Grinding media additives are used to optimize the vibratory finishing process. They can contain cleaning agents, polishing agents, corrosion inhibitors, and other additives that improve surface processing.
Water acts as a lubricant and contributes to cooling, thereby reducing friction and heat development during the grinding process.
The choice of abrasive media affects the intensity of the grinding process, the quality of the surface, and the type of processing, such as deburring, polishing, or edge rounding.
Abrasive additives improve the effectiveness of the grinding process by performing cleaning functions, affecting the surface quality, or providing protection against corrosion.
There is no one-size-fits-all solution. The composition of abrasive additives is tailored to the specific requirements of each process and the workpieces to be processed.
The amount of process media depends on factors such as the size of the grinding drum, the type of workpieces, and the desired processing results.
It is important to wear suitable protective equipment such as gloves and safety glasses to minimize potential hazards when handling abrasives and abrasive additives.
Summary:
The successful application of vibratory finishing relies on the targeted use of various process media. Grinding bodies, grinding media additives, and water are the core elements of this process. The selection and combination of these process media play a crucial role in achieving the desired surface quality, whether through deburring, polishing, or edge breaking of workpieces. The following section sheds light on fundamental questions regarding the process media in vibratory finishing, providing a deeper understanding of their functions, applications, and properties.
Basics of Induction Technology:
10 Key Questions from the Industry Answered
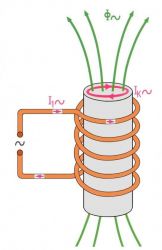
Induction technology is based on the principle of electromagnetic induction, where an electrical voltage is induced in a neighboring conductor (workpiece) by a changing magnetic field.
Image source: J. Fasholz et al.: Inductive Heating. Process Information, Essen: RWE Energy, 1991.
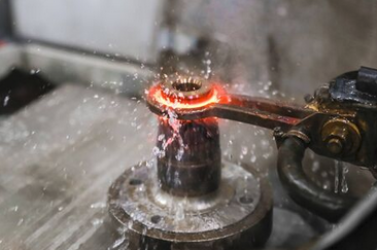
In industry, induction technology is primarily used to heat metallic materials for processes such as hardening, melting, welding, joining, and loosening, as well as for soldering, heating, and annealing.
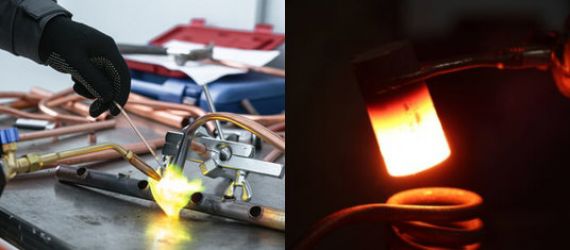
Induction heating is often faster, more precise, more efficient, and provides better control over the heating process. The energy input is consistent and reproducible. There are also no direct flames, which is often safer.
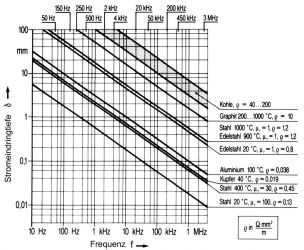
Frequency is crucial for the penetration depth of the magnetic field into the material. Higher frequencies produce a shallower penetration depth (also called the skin effect), which is suitable for thin workpieces, while lower frequencies penetrate deeper, suitable for thicker materials.
Image source: J. Fasholz et al.: Inductive Heating. Process Information, Essen: RWE Energy, 1991.
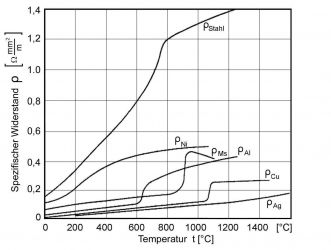
The effectiveness of inductive heating strongly depends on the electrical and magnetic properties of the material. Materials with higher electrical conductivity and permeability, like many metals, heat up faster. Non-conductive materials, such as most plastics, are less suitable for induction heating unless they contain conductive fillers.
Image source: G. Benkowsky: Induction Heating. Hardening, Annealing, Melting, Soldering, Welding. Verlag Technik Berlin, 1990.
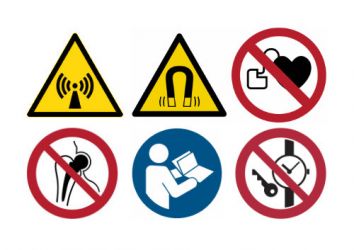
When properly used, induction technology is safe. However, due to the high temperatures and strong magnetic fields involved, safety precautions and training are required.
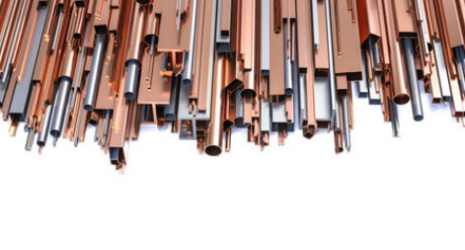
Many metals, especially conductive materials such as steel, copper, and aluminum, as well as silver, gold, and brass, can be thermally treated using induction technology. However, efficiency can vary depending on the material.
Induction heating is often more energy-efficient than traditional methods because it directly heats the workpiece and not the environment, minimizing energy losses, leading to a reduction in CO2 emissions and other environmental impacts, especially when powered by renewable sources.
Induction technology allows for faster and more precise heating of materials, leading to shorter process times and reduced energy consumption. Targeted and even heating can maintain higher quality standards and reduce scrap, thereby increasing overall productivity.
Limitations include the need for a conductive material, the limited penetration depth of the magnetic field, and the requirement for specialized equipment and training.
Summary:
In the multifaceted world of industrial technology, induction technology has taken a special place. The basic principle relies on generating an electrical voltage in a neighboring conductor (workpiece) through a changing magnetic field. This technique is primarily used in the industry for heating materials for various processes, including hardening, melting, welding, joining, soldering, heating, and annealing. A significant difference from conventional heating methods is the type of energy transfer. In induction heating, the transfer is done directly to the material through a changing magnetic field, while traditional methods often transfer heat through direct contact, radiation, or convection. In this type of heating, frequency plays a key role. Depending on whether a high or low frequency is chosen, the penetration depth of the magnetic field varies, directly affecting the heating efficiency of the target material. The efficiency of induction heating itself strongly depends on the electrical and magnetic properties of the material to be heated. Particularly conductive materials, like many metals, respond especially well to induction heating. In terms of productivity, induction technology proves superior, allowing for faster and more precise heating, leading to shorter process times and reduced energy consumption. From an environmental perspective, induction technology can contribute to reducing the CO2 footprint, especially when powered by renewable sources.
Diving into the World of Painting Technology:
The essential 10 questions and their corresponding answers in the field of painting technology.
Painting technology refers to the field of expertise dealing with the application of paints, colors, and coatings on surfaces to provide protection, aesthetics, and functionality.
The primary objectives of painting technology are surface protection, aesthetic enhancement, increased durability and resistance, and the implementation of functional properties such as rust protection or conductivity.
There are various types of painting systems, including spray booths, immersion baths, powder coating systems, and robotic systems.
In wet painting, liquid paint is sprayed onto the surface, while in powder coating, fine powder is electrostatically applied and then fused into a coating by heating.
The quality of a paint job is influenced by factors such as surface preparation, correct paint selection, uniform application, drying, and curing.
Proper pre-treatment, such as cleaning, degreasing, and derusting, ensures that the paint is applied to a clean and adhesive surface, guaranteeing good adhesion and durability.
Drying is crucial to harden the paint film and optimize its mechanical and chemical properties.
Dry and wet fog separators are systems that filter excess paint mist from the air, protecting the environment and ensuring workers' health.
Automating painting systems increases the consistency, precision, and efficiency of the painting, reduces resource consumption, and the error rate.
In painting systems, good ventilation systems, personal protective equipment such as respirators and protective suits, and fire protection measures are vital to ensure worker safety and minimize fire risks.
Summary:
Fascinating world of painting technology! This versatile field deals with the precise application of colors, coatings, and paints on surfaces, not only enhancing their aesthetics but also optimizing their durability and functionality. From basic techniques to state-of-the-art automation systems, painting technology offers a wide range of approaches used across various industries to protect, beautify, and refine products. Here, we take a look at the key questions and answers that will give you a comprehensive insight into this exciting field.
Special Machine Engineering:
Custom solutions for individual industrial requirements in 10 questions and answers:
Special machine construction is an area of mechanical engineering that focuses on the development, design, and manufacturing of tailor-made or specially adapted machines and systems for individual company requirements.
Special machine construction is used in many industries, including the automotive industry, food and beverage industry, pharmaceuticals, packaging industry, electronics manufacturing, and more.
Special machines offer the advantage of being precisely tailored to a company's specific requirements, which can lead to higher efficiency, product quality, and competitiveness.
The steps include: Requirement analysis, concept development, design, manufacturing, assembly, commissioning, and quality inspection.
Factors to consider include customer requirements, technical feasibility, safety, ease of maintenance, cost, and possible scalability.
Automation and robotics play a crucial role in enhancing the efficiency and precision of special machines, especially in areas like assembly, packaging, and testing.
In the automotive sector, special machine construction enables the creation of automated production lines and testing systems that accelerate the assembly process and ensure vehicle quality. Special machines can also be used in the development and manufacturing of prototypes and special vehicles to meet specific requirements.
Digitization enables the simulation of designs, virtual testing, remote monitoring of plants, and the integration of Industry 4.0 principles to optimize production processes.
Challenges include complex requirements, tight schedules, high costs, integrating different technologies, and ensuring compliance with safety standards.
Regular maintenance of special machines is crucial to ensure optimal performance, longevity, and safety and to minimize unplanned downtimes.
Summary:
Special machine engineering is at the heart of tailor-made industrial technology, enabling companies to develop specially adapted solutions for their unique requirements. In an ever-evolving economic world where efficiency and precision are paramount, special machine engineering plays a key role in designing and manufacturing custom production plants and automation systems. From the automotive industry to food processing, this field opens up new horizons for innovation, flexibility, and competitiveness. Let's take a closer look at the world of special machine engineering, its significance, its applications, and the challenges associated with it.
Basics of Automation Technology:
All you need to know about automation technology summarized in 10 questions
Automation technology refers to the application of technology to control, monitor, and optimize processes or systems, minimizing human intervention.
Automation technology provides benefits such as increased efficiency, lower error rates, improved product quality, consistent production, and faster response to changes.
There are three main types of automation:
- Manufacturing Automation: Automation in the production of goods.
- Process Automation: Automation of continuous processes like chemical production.
- Building Automation: Automation of systems within buildings, such as climate and lighting control.
Sensors detect physical quantities like temperature, pressure, or position and convert them into electrical signals that can be processed by automated systems.
A PLC (Programmable Logic Controller) is a computer used in industrial applications, processing digital and analog inputs and outputs to control machines and processes.
Robots are widely used in automation technology and are deployed to perform tasks across various industries, from manufacturing to logistics.
In open-loop automation, actions are executed without feedback, while in closed-loop automation, information about the system state is used to make adjustments.
Networking allows different devices, machines, and systems to connect, exchange data, optimize processes, and enable remote monitoring and control.
Industry 4.0 is a concept integrating advanced technologies such as the Internet of Things, artificial intelligence, and big data analytics into industrial production to create intelligent factories and optimized workflows.
Some challenges include vulnerability to technical malfunctions, the need for qualified professionals, the security of networked systems, and the impacts on jobs due to automation.
Summary:
Automation technology forms the backbone of modern industries and processes by leveraging technology to automate and optimize manual operations. This fascinating discipline is transforming how we produce, control, and interact. From manufacturing goods to regulating complex processes, automation technology enables more efficient and accurate workflows. In this context, the following delves into fundamental questions about automation technology, shedding light on its importance and applications.
Basics of Conveying Technology:
Conveying Technology in Focus, 10 Questions and Answers for Beginners
Conveying technology encompasses all technologies, devices, and systems designed to efficiently transport materials or products within businesses, production facilities, or warehouses.
There are various types of conveying technology, including roller conveyors, conveyor belts, forklifts, cranes, elevators, pneumatic and vacuum conveyors.
Using conveying technology increases efficiency, reduces costs, minimizes manual labor, reduces material loss, and enhances workplace safety.
Key points in planning include the type of materials to be conveyed, the required conveying speed, spatial conditions, energy efficiency, and safety aspects.
A conveyor belt consists of an endless loop that runs over rollers or support rollers. A motor drives the rollers, causing the conveyor belt to move and transport material from one point to another.
Automation plays a crucial role as it allows controlling material flow without human intervention. Automated conveyor systems can optimize material transport and reduce the need for manual labor.
Gravity roller conveyors use the principle of gravity to transport materials on slightly inclined conveyors without the need for an external power source.
A pallet conveyor is a special type of conveyor belt or roller conveyor designed to transport pallets with goods, typically in storage or production environments.
In conveying technology, safety measures such as emergency stop switches, protective barriers, light barriers, and employee training are crucial to prevent accidents.
Conveying technology plays a key role in logistics by ensuring the smooth transport of goods in warehouses, distribution centers, and shipping areas, in turn contributing to the efficiency of the supply chain.
Summary:
Conveying technology forms the backbone of many industrial processes and logistical operations. It encompasses a wide range of technologies, devices, and systems aimed at efficiently moving materials and products from one place to another. From conveyor belts and gravity roller conveyors to automated robot systems, conveying technology plays a pivotal role in streamlining production and storage processes. In this article, we take a look at the basics of conveying technology by answering 10 frequently asked questions to provide a better understanding of its functioning, benefits, and applications.
Want to know more?
If you haven't found the right question on our IPS FAQ page or wish for a more in-depth discussion on the various topics, we are here for you.
We offer not only answers but also personal conversations.